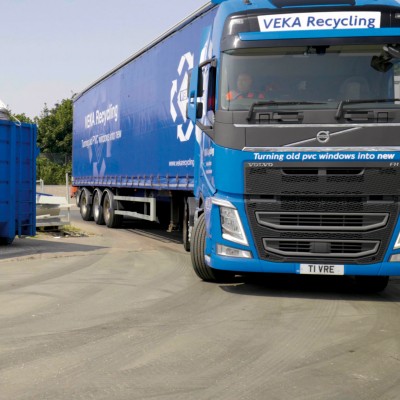
VEKA Recycling Opens Northern Hub, Introduces Glass Collection Pilot Scheme
Press information
As part of the company’s ongoing commitment to drive the efficiency and sustainability of its PVC-U recycling service, VEKA Recycling has opened a Northern consolidation hub, whilst also introducing IGU collection through a pilot scheme.
Based in Burnley, Lancashire, the VEKA Recycling hub will consolidate materials, collected throughout the north of England and Scotland. Material, including old PVC-U windows and virgin offcuts from frame fabricators producing windows and doors manufactured from various systems, will be collected and sorted at Burnley. The PVC-U and other materials will then be moved on in bulk by VEKA Recycling’s fleet of vehicles. This will further improve the logistical substantiality of the process, which for VEKA Recycling is already impressive due to the central UK location of its processing plant.
The hub will also facilitate the collection and drop-off of material using smaller vehicles in Burnley and surrounding areas. VEKA Recycling’s hub will provide a convenient and inexpensive way of disposing of old PVC-U frames for local installers.
In a further initiative designed to improve the ease by which installers may present old frames for recycling, VEKA Recycling will also introduce a pilot scheme to collect old IGUs with the frames. This is expected to boost the number of PVC-U frames returned for processing significantly. The cullet will then be returned to a glass manufacturing partner to be made into new flat glass. This material uses around 30% of recycled material in its manufacture. The scheme will be customised to the customer’s needs, thus further simplifying the process of returning PVC-U and other materials for recycling.
Commenting on the PVC-U and recycling initiatives, managing director of VEKA Recycling Ltd Stuart Stockley said: “VEKA Recycling processes everything collected in the UK at its Midlands processing plant, the most advanced in Europe. In itself, this is more efficient than many other recyclers because it reduces the miles driven to return the old frames to the point of recycling. Plus, the complex process of turning the old frames into new polymer is completed within the same facility. Often, the material is processed in a number of stages, at different plants. We do everything in-house.
“The return of old insulated glass units as part of the disposal process is a big step forward to take hassle away from our customer simplify the return of material,” added Stuart.
“The recycling of old PVC-U window and door frames has long been established – VEKA built the first plant for the purpose as far back as 1993,” he explained. “But whilst we are experts in the processing of PVC-U, today there is far greater emphasis on holistic sustainability. These initiatives further address that requirement.”
If you are interested in recycling your old PVC-U frames with VEKA Recycling, then please don’t hesitate to contact us today. Our team will be happy to provide more information about our PVC-U recycling services. Start your PVC-U recycling process today!
Prepared by VAST PR on behalf of VEKA Recycling Ltd. For further information contact Beth Brennan at VAST PR, on 0845 0945 215; email beth@vastpr.co.uk. August 2023.
Notes for editors:
VEKA Recycling Ltd is part of the VEKA Group, the world leader in the field of PVC-U profile systems manufacture, and has pioneered the recycling of PVC-U material since 1993. With a UK headquarters located in Wellingborough, VEKA Recycling works with fabricators, installers and waste companies throughout the UK to ensure that valuable PVC-U material is not lost to landfill.
VEKA Recycling’s innovative and advanced processes ensures that old windows and doors are recycled and extruded into new windows and doors and a range of other products, that boast the same standard of quality as the originals. The company is committed to sustainability by ensuring that every stage of its closed loop process is as environmentally friendly as possible.