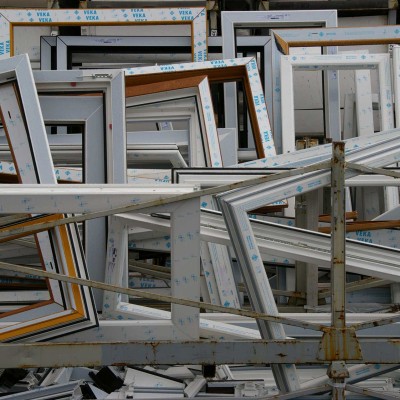
Flying the flag for recycled plastics
Veka Compounds highlights the need for solid audit trails, quality recycled goods and unproblematic availability to drive plastics forward in the new world of sustainability.
According to WWF, 83% of PVC-U ends up in a landfill. This is entirely unacceptable, considering the material can be recycled up to fifteen times with no loss of structural integrity. Global brands and individual consumers alike are becoming increasingly aware and determined to take action to reduce their environmental impact by taking a stance on sustainability. So, for PVC-U to continue to be part of the conversation, the industry needs to close the loop on its recyclability.
The continued drive towards sustainability is putting mounting pressure on processors to be sustainable and to be seen to be sustainable, but there have historically been factors delaying progress. Technical and logistical barriers to sourcing recycled compounds mean we’re not as far forward as we should be in achieving a flawless circular economy where plastic goods are concerned.
Post-consumer and industrial PVC-U is a niche sector within rigid plastics that is dominated by the home improvement replacement window and door industry. It is a sector that has made excellent inroads into recycling goods, with approximately 80% of windows and doors removed from dwellings being sent to be recycled. But the cycle breaks down when the recycled compound offered back to processors has been found to be inconsistent in its quality and in its availability. Much of it also comes from unknown and unaudited sources. Only by bridging this gap, will the sector achieve the necessary sustainable credentials.
VEKA Recycling Ltd – sister company of VEKA Compounds – is doing its bit with what is reputed to be Europe’s most advanced facility to recycle old PVC-U window and door frames, located at Wellingborough, Northamptonshire. The facility was established to address this very issue.
Managing Director of VEKA Recycling Ltd, Simon Scholes, explains: “By professionalising the recycling of PVC-U we need to remove any doubts about integrity. When we have made the recycling of PVC-U unremarkable, we will have accomplished the remarkable. The only way this can be done is through achieving consistent quality, a solid audit trail, and precision throughout the cycle.”
The numbers read well for the Wellingborough facility: the company’s most popular pellet is Grey white 9002.001, which shows Impurities of <0,02%; Colour L 89 (+1); and Apparent density of ≈0,85 g/cm3. But whilst these figures are impressive, it is the consistency with which these standards are delivered that is the breakthrough, says Simon: “The VEKA Recycling Ltd commitment is that our compound can be trusted to perform reliably due to our focus on high quality and that it will always be available thanks to our incredible capacity. We can also deliver to processors on time because we are handling the product entirely within our own facility in the UK. Keeping the process in one place further improves the quality with fewer logistical and contamination challenges to overcome. Another key element is that we control the entire procedure ourselves so that we know precisely what has gone into the process, how the product has been handled, and what is coming out the other side, which few companies in the UK are able to do. It is always worth asking about the trail as part of your own quality control check.”
PVC-U is an extraordinary and valuable resource. But it will only ever be viewed as sustainable if it can be returned to the market for re-manufacture again and again. Then its true value will be realised, and that can only be achieved if it is re-processed consistently to enable this to become a commercial reality. VEKA Compounds and its sister company VEKA Recycling appears to have achieved just that as it continues to fly the flag for recycled plastics.